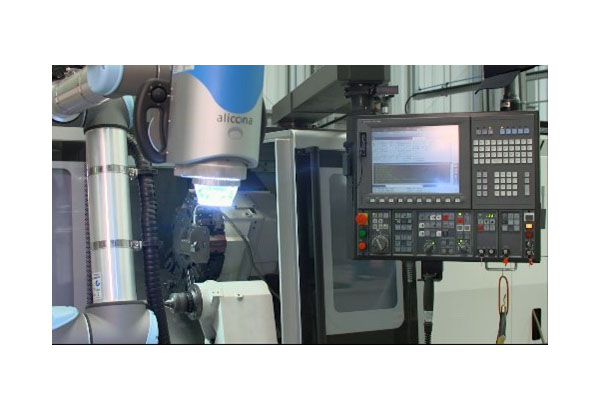
Helping Element6 make improvements and efficiencies in the cutting tool development process
Element 6 is a leading manufacturer of machine tools that works with customers from the automotive, aerospace, and mechanical engineering industries. They sought to improve critical test factors for higher performance and longer life. One of their particular specialisms is the use of polycrystalline cubic boron nitride (PCBN) as a base material and machining speeds of 300 m/min, offering predictable wear behaviour and up to 50% longer tool life in hardened steel machining. They came to Optimax to explore the latest methods and tools to offer even more improvements and automation, especially as the measurement of tool wear was a procedure that could be time-intensive. (Traditionally, the measurement involves a predetermined number of cuts or a specified time before assessing wear.)
Automatic, in-situ wear measurements offer the solution
We recommended implementing an automated test program with Bruker Alicona and the collaborative measuring system CompactCobot. Using this combo, the tool and workpiece surface finish are measured in a fully automated process directly in the lathe. Now, wear measurements could be seamlessly conducted within the lathe between cuts. This innovation not only streamlined the measurement process but also gave the potential to optimize the overall performance and longevity of cutting tools. Automatic, in-situ wear measurements are a more dynamic way of getting a real-time understanding of tool performance, allowing for timely adjustments and informed decision-making in the cutting tool development process.
At a defined point, the lathe stops, the door opens, and the Cobot is instructed to carry out a measurement sequence comprising dimensions and surface roughness. The robot arm withdraws, and the measurement and surface profiling data are used to determine whether the insert is in tolerance. If it is not, the machining parameters are adjusted, and the part is machined and then measured again. This ensures that every part, including the first, is good.
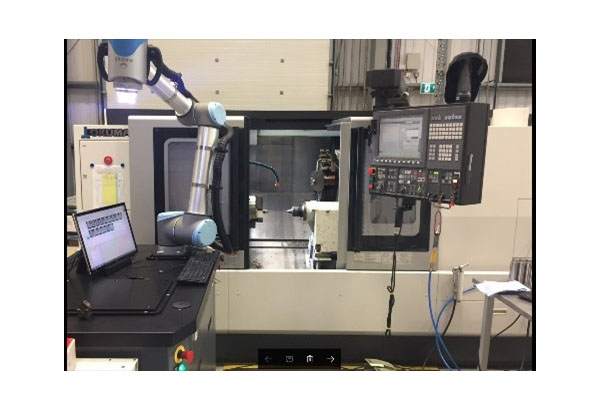
Compact cobot fitted with a R25 optical sensor
We recommend the compact cobot fitted with an R25 optical sensor and integrated with a CNC automatic lathe. The two systems work together to assess tool wear after each cut. The Compact Cobot, an optical collaborative measuring system, facilitates integration and networking in several ways. Its robustness ensures high-resolution measurements with speed and repeatability, even in a production environment. The Automation Manager allows for automated unmanned measurements during production.
The Compact Cobot has interfaces like TCP/IP, Modbus/TCP, or Anybus, enabling seamless connection to existing production systems. This integration fosters communication between machines, contributing to the realization of a self-controlling, self-correcting production environment.